Incorporating the right quality control techniques is crucial for businesses aiming to ensure high product standards, minimize defects, and streamline processes. From traditional inspection methods to advanced statistical approaches, quality control techniques provide structured ways to enhance product quality and maintain consistency. This article explores essential QC methodologies, such as Six Sigma and Lean principles, and newer approaches that empower companies to meet and exceed quality expectations.
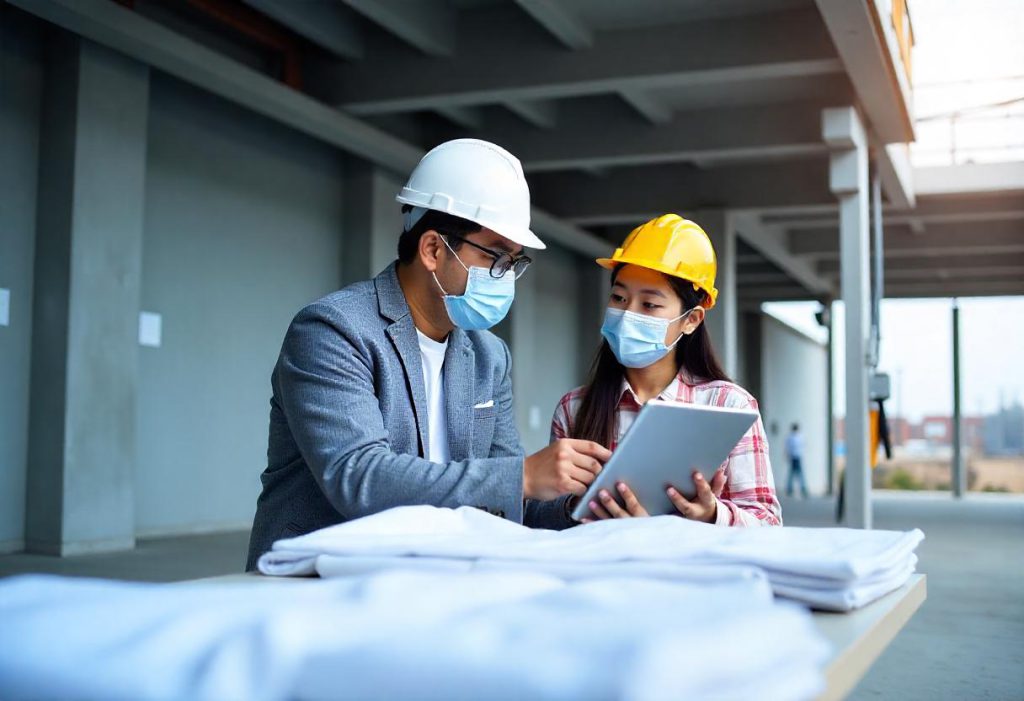
Statistical Process Control (SPC)
Statistical Process Control is a widely-used QC technique that relies on data and statistical methods to monitor and control processes. By using control charts and analyzing process data, companies can identify patterns and prevent defects before they occur. SPC’s data-driven approach makes it ideal for tracking production quality over time.
The Role of Six Sigma
Six Sigma is a systematic methodology focused on reducing process variation and eliminating defects. Using tools like DMAIC (Define, Measure, Analyze, Improve, Control), Six Sigma aims to achieve near-perfect quality by reducing errors to no more than 3.4 defects per million opportunities. Companies implementing Six Sigma find that it improves both quality and efficiency, making it an invaluable tool in quality control.
Lean Manufacturing for Waste Reduction
Lean manufacturing prioritizes waste reduction and value maximization in production. By identifying and eliminating non-value-added activities, Lean helps companies improve quality and efficiency. Techniques like 5S (Sort, Set in order, Shine, Standardize, Sustain) support organized, streamlined workplaces that reduce errors and facilitate smoother QC processes.
Failure Mode and Effects Analysis (FMEA)
FMEA is a preventive tool that identifies potential failure points within a process and assesses their potential impact. By examining every aspect of a product’s life cycle, FMEA helps teams proactively address vulnerabilities. This ensures that all possible points of failure are controlled, resulting in improved product reliability.
The Value of Total Quality Management (TQM)
Total Quality Management is a comprehensive approach that engages every level of an organization in the quality control process. TQM emphasizes a culture of continuous improvement and customer satisfaction, using tools like benchmarking and Kaizen (continuous improvement) to drive quality across all functions.
Root Cause Analysis (RCA) for Problem Solving
When quality issues arise, Root Cause Analysis helps identify the underlying causes. By understanding why a defect or failure occurred, companies can implement solutions that prevent future issues. RCA techniques like the 5 Whys and Fishbone Diagram are effective for systematically investigating problems and maintaining QC consistency.
Quality Assurance (QA) in Parallel with QC
Quality assurance complements QC by focusing on improving processes to prevent defects. QA emphasizes setting standards, conducting regular audits, and continuously refining processes. While QC inspects the final product, QA ensures processes are optimized to deliver consistent quality.
Incorporating Advanced QC Software
QC software streamlines data collection, inspection, and analysis. Using digital tools allows companies to track quality metrics in real time, identify patterns, and make informed decisions. Advanced QC software is invaluable for managing complex data, especially for companies with large-scale operations.
Implementing ISO Standards for Quality
Adhering to international standards, such as ISO 9001 for quality management, provides a structured framework for QC. These standards help companies align with industry best practices and assure customers of consistent quality.
Continuous Improvement and Innovation in QC
Continuous improvement methodologies like PDCA (Plan-Do-Check-Act) drive long-term quality improvements by encouraging teams to regularly evaluate and refine QC processes. Adopting a mindset of innovation allows companies to adapt their QC practices to changing industry needs.
Conclusion
By integrating these quality control techniques, companies can build more reliable QC systems, reduce waste, and achieve superior product quality. From statistical methods to continuous improvement practices, each QC methodology plays a role in maintaining high standards and helping companies meet customer expectations. Embracing both foundational and innovative techniques empowers organizations to deliver consistent quality and maintain a competitive edge.