In today’s competitive market, quality control best practices are essential for companies aiming to maintain consistent product quality and build customer trust. Effective quality control (QC) processes help minimize defects, optimize production, and ensure that products meet regulatory standards. In this article, we’ll explore key practices and techniques that companies can implement to improve their QC processes, boost efficiency, and deliver higher quality to their customers.
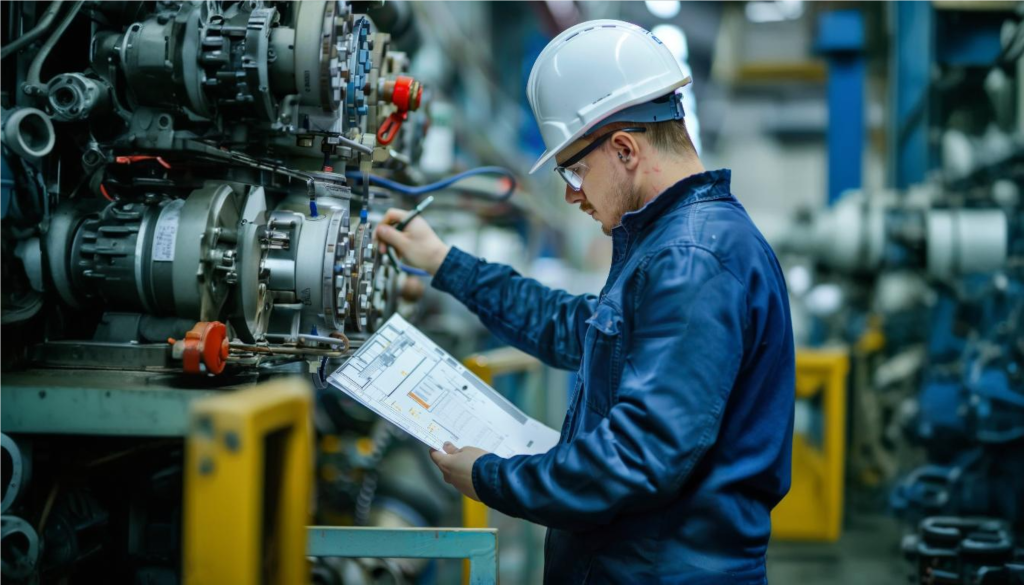
Establish Clear Quality Standards
The foundation of quality control lies in establishing and documenting clear quality standards. This includes setting measurable criteria for product characteristics such as dimensions, performance, and durability. By defining these standards upfront, companies can align production processes and ensure each stage meets specific quality benchmarks.
Implement Regular Inspections and Testing
Frequent inspections and product testing are crucial to catching defects early. This can include in-process inspections, where quality checks are performed during production, and final inspections after assembly is complete. Adopting rigorous testing practices, such as statistical process control (SPC) and random sampling, helps identify variances and maintain quality consistency.
Leverage Technology in QC Processes
Modern QC methods now incorporate advanced technologies like automated inspection systems and data analytics. Automated inspection tools use sensors, cameras, and software to detect defects with high accuracy. Data analytics, on the other hand, can analyze production trends and identify recurring quality issues, allowing proactive adjustments.
For more information you can refer to Wikipedia’s introduction through here.
Engage in Supplier Quality Management
Quality control extends to the suppliers who provide raw materials and components. Companies should conduct supplier audits to evaluate suppliers’ quality practices and ensure they meet required standards. Building strong relationships with suppliers helps maintain a consistent quality level throughout the supply chain.
Train Employees on Quality Control Procedures
Employee training is vital for effective quality control, as well-trained staff are more likely to adhere to established QC procedures. Training should cover specific quality standards, inspection methods, and corrective action processes. Engaging employees in quality initiatives can lead to a more quality-focused culture within the organization.
Implement Continuous Improvement Practices
Continuous improvement is a core principle in QC, where companies constantly seek ways to enhance quality. Techniques like Lean manufacturing and Six Sigma provide frameworks for identifying inefficiencies, reducing waste, and improving product quality. By continuously monitoring QC processes and implementing small improvements, companies can achieve significant quality gains over time.
Establish a Corrective and Preventive Action (CAPA) System
A Corrective and Preventive Action (CAPA) system is a structured approach to addressing quality issues. When defects are detected, CAPA processes analyze the root cause, implement corrective measures, and take preventive actions to avoid recurrence. CAPA is a powerful tool for maintaining long-term quality consistency.
Use Quality Control Software for Process Management
Quality control software provides a centralized platform for managing QC data, tracking inspection results, and analyzing trends. This software streamlines QC operations, making it easier to monitor quality metrics and share data with stakeholders. With real-time data access, companies can make faster, data-driven decisions to enhance QC effectiveness.
Standardize Documentation for Quality Audits
Consistent documentation is essential for quality audits and regulatory compliance. Standardized forms, checklists, and records help maintain uniformity in QC processes and make it easier to review performance. Well-organized documentation also simplifies audits by providing clear evidence of QC practices.
Conduct Regular Quality Audits
Quality audits assess the effectiveness of QC processes and ensure that standards are consistently met. Companies can perform internal audits to evaluate their own processes and external audits to verify supplier quality. Audits provide valuable insights into areas needing improvement, helping companies refine their QC practices.
Conclusion
Adopting these quality control best practices enables companies to streamline their processes, minimize defects, and consistently meet customer expectations. By focusing on proactive inspections, supplier management, employee training, and continuous improvement, organizations can achieve higher quality standards and foster long-term customer satisfaction.